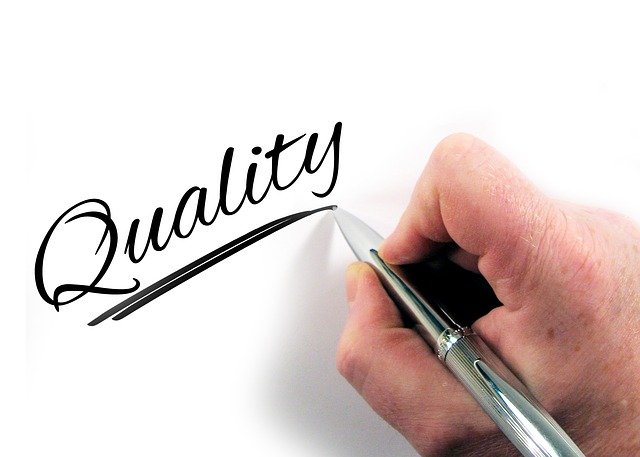
The Quality Management System
The Quality Management System (QMS) is the most important system in a business. In fact, it is the backbone of any business that keeps everything together and moving in the right direction at a quality acceptable to your clients and customers. How strange then that most small businesses do not have a QMS in place. It is unfortunately one of those things that business owners feel they do not have the time to put in place when they just start out. When it comes to bite them, they run around, madly trying to put it in place because, truth to tell, they still do not have time, but by then, they already have a monster on their hands and it is difficult to tame.
So what exactly is a Quality Management System? Let’s start by first defining quality. There are many different definitions for quality but as business owners we are interested in two. Firstly, quality has to do with the specific attributes of something, whether a product or a service. Secondly, it has to do with “a degree or grade of excellence or worth“. As business owners we can summarize this as “meeting or exceeding the customer’s expectations”. This is very important. Because a happy customer is a returning customer.
Elements to Quality
There are two elements to quality. Both are equally important: repeatability and reproducibility.
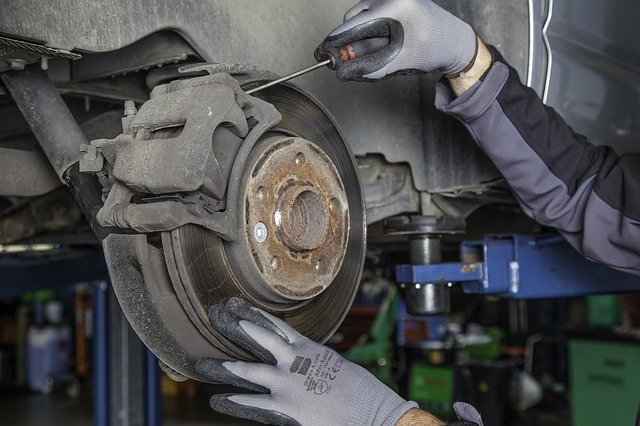
Repeatability is the ability to get more or less the same test results every time you test your product. We are talking about one product here. Let’s look at a simple example. Say I am building cars. Every time I test the quality of the brakes, I want to get the same result, never varying. This car’s brakes must have the same efficiency after having been used a hundred times that it had after its first use. It means that they test those brakes many, many times to determine when they start deteriorating and then they inform the customer that the brakes have to be replaced by a certain number of kilometres, well before they start deteriorating. To go back to our definitions, you want to define the attributes that give your product or service its worth or degree of excellence. This is what repeatability gives you.
Once you have repeatability, you need reproducibility. What is needed to reproduce the product or service over and over again with the same attributes and the same degree of worth?
Continuous Improvement
Add to this continuous improvement and then you will understand what a Quality Management System is. Continuous improvement does not only want the same results, it wants those results to be improving. This means that you should continually be monitoring what you are doing and then act on what you are seeing.
Plan
What you need to understand is that you can know what you need to do but unless you intentionally make a plan and write it out, it will not happen. This is what a Quality Management System is. The plan you make and implement to meet or exceed your customers’ expectations.
Can you see why it is so vital to your business?
Procedures
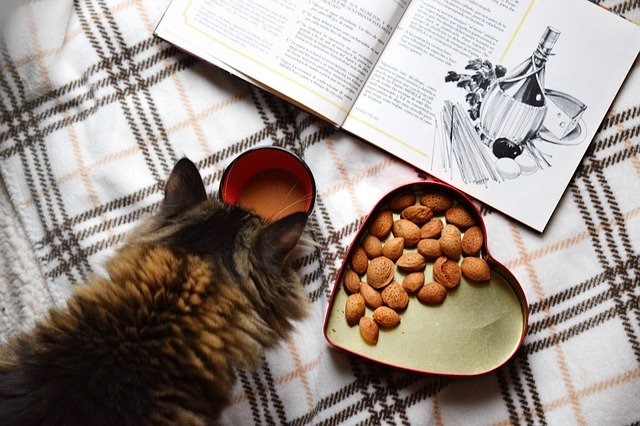
To ensure repeatability and reproducibility a business needs procedures. Procedures are like a recipe. It tells you what the ingredients or raw materials are that you need. In this day and age it also identifies the safety procedures you have to follow. Then it tells you step-by-step the actions you need to take.
Traceability
There are many different quality management systems today, e.g. Total Quality, Six Sigma, and ISO 9000. For some, like ISO 9000, your business can even get accreditation. This can be very daunting to a small business owner. They see the expense involved and then simply throw in the towel. What you need to understand though is that many big businesses require that their suppliers must have some sort of QMS. It does not necessarily have to be accredited but it must be recorded. This means that it must be a written plan that provides traceability. Traceability involves tracking the process that my product/service went through from beginning to end. I can show where the quality was checked and I have the records to prove it.
Quality Assurance
Quality is checked at least three times during the process.
At the Input Stage
This is where supplier quality comes in. If you know that your supplier has some sort of QMS, you do not need to spend so much time in checking input quality. But you still need to verify the quality of your raw products or whatever goes into your service. If, for example, your service is to provide training this would be the time to check your training materials. If you are building, this is where you will make sure the building materials comply with regulations.
During Operations
Depending on your product or service there can be one or many quality checks during production or service rendering. You want to make sure that you are still on track. It can be a test or homework during training. This would be when you take out your plumb line, water level and measuring tape during construction. Or where you would run laboratory tests from the production line. If there are different stages during production/service, it works well to check quality at the end of every stage.
At the Output
Before you send your product away or sign off on your service you must make sure that it complies with what you promised to deliver. So, you test it again. It is here where you provide a Certificate of Compliance. A COC is the proof that what you provide complies with your own QMS requirements and that your product or service is what you offered to provide. You have to be so certain of this that your customer can come back if there is a product failure. A business’ reputation is established when the supplier experiences a product failure and they do not suspect the materials you supplied because your materials never fail.
Is Quality Possible?
Is it possible for a small business to ensure a quality service or product? Yes. Is it affordable for a small business to implement a Quality Management System? Yes. Can your business afford to go without Quality Management? No.
If you need help with a QMS for your business or advice about it, contact us.